LES CLES DU DIMENSIONNEMENT
Ouvrages en commandePhotovoltaïque autonome
Photovoltaïque raccordé au réseau
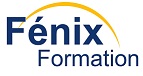
Formations Professionnelles Photovoltaïques
Lampes fluorescentes > Veillissement : généralités
Avant de recenser les résultats de la recherche bibliographique il est nécessaire de donner quelques définitions et de décrire le procédé de fabrication qui va jouer un grand rôle dans la durée de vie des lampes.
Définitions
Durée de vie moyenne
La durée de vie moyenne est le nombre d’heures pour lequel la moitié des lampes d’un groupe représentatif est arrivée en fin de vie. Cette définition autorise une dispersion autour de la valeur moyenne qui peut être dans certain cas très importante.
Maintenance du flux lumineux
La maintenance du flux lumineux est le rapport entre le flux lumineux à un nombre d’heure de fonctionnement donné et le flux lumineux initial émis par une lampe. Cette quantité est exprimée en pour cent.
Durée de vie de service
La durée de vie de service est définie comme le produit entre la durée de vie moyenne et la maintenance du flux lumineux.
Principe de fabrication
Les phénomènes de vieillissement sont fortement liés à la technologie de fabrication des lampes, à la nature et la qualité des matériaux utilisés ainsi que les différents processus d’activation comme la transformation des carbonates de baryum en oxyde. Les principaux éléments constitutifs et leurs assemblages sont décrits dans ce paragraphe.
La fabrication des lampes fluorescentes nécessite d’abord la préparation de matière fluorescente. Celle-ci se présente sous la forme de poudre à grains parallélépipédiques obtenus par broyage à 10 m. Les principaux produits de bases µ sont généralement :
- les halophosphates de calcium activés à l’antimoine ou au manganèse,
- le silicate de calcium activé au plomb ou au manganèse,
- le phosphate de strontium et de magnésium activé à l’étain,
- le fluogermanate de magnésium activé au manganèse,
- le vanadate de d’yttrium activé à l’europium,
- les aluminates de magnésium activés au baryum, à l’europium, au cérium ou au terbium.
Ensuite, la préparation des tubes commence par un rétreint des extrémités au diamètre de l’envasement du pied. Après lavage des tubes, des couches de matière fluorescente sont déposées par montée puis descente de la suspension liquide. Un séchage (pour éliminer le solvant) puis un passage au four (pour éliminer le liant) sont ensuite effectués. Enfin, un brossage interne des extrémités du tube est réalisé, de manière à enlever les poudres situées dans la zone de scellement du tube avec les pieds.
Pour le montage des pieds et des électrodes, les entrées de courant qui servent de support et une tige de dumet destinée à soutenir l’anneau de garde, sont insérées dans le verre entre les entrées de courant.
La fabrication des électrodes commence d’abord par le spiralage des filaments autour de mandrins successifs, de différents diamètres, de manière à constituer une cage spiralée autour d’une spirale centrale. Ces mandrins, constitués de molybdène, sont ensuite dissous pour laisser apparaître le filament sous sa forme définitive. La partie centrale de l’électrode, qui constitue sa partie active, est ensuite plongée dans un bain composé d’un mélange de carbonate de baryum, de strontium, de calcium et de zirconium. Cette partie centrale est ensuite sertie à deux filaments de Fer-Nickel permettant de relier les électrodes au circuit électrique extérieur. Suivant la puissance des tubes, un ruban annulaire en nickel ou en acier nickelé est soudé autour du filament sur le fil de dumet. Cet anneau sert à éviter le dépôt de matériel émissif sur la paroi interne du tube et permet aussi de contracter la décharge en phase anode facilitant ainsi la collecte électronique. Enfin, sur une des deux électrodes, une petite capsule contenant du mercure est sertie sur la coupelle. On peut voir une telle structure sur la Figure I-11.
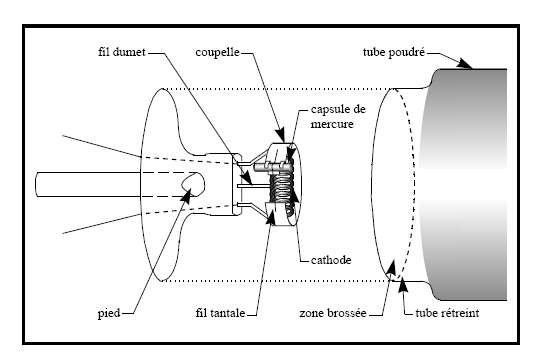
Figure I-11 : Pied avec électrode et capsule de mercure
Les pieds sont présentés des deux cotés du tube placé horizontalement, les évasements venant toucher les bords du tube. Le scellement se fait par ramollissement de l’ensemble (il n’y a pas étirage du tube).
Le pompage se fait par deux queusots sur une machine à axe horizontal. Il commence par une succession de rinçages avec de l’argon suivis de vidages. Ensuite un remplissage final à très faible pression d’argon ou d’un mélange de gaz rare est effectué. Enfin les queusots sont refermés.
Avant le culottage et l’emballage (finition), le fil de tantale est chauffé sous l’action d’un champ haute fréquence, ce qui provoque une fissure de la capsule de verre, et le mercure se vaporise alors dans le tube.